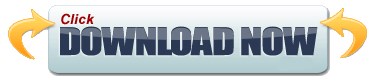

Here, we look at some of the advances and changes-in technology and, perhaps as important, in manufacturing mindset-that will be necessary to achieve LAM’s game-changing potential. Yet in many ways, LAM today, for reasons related to cost and technology bottlenecks, remains a niche manufacturing approach. Such investment suggests that LAM could be at the proverbial “hockey-stick” take-off point for rapid development. Indeed, investment in additive manufacturing has increased from a few tens of millions of dollars a decade ago to several hundred million dollars today, with companies like General Electric, Siemens and Aerojet Rocketdyne leading the way. Under intense development for the last decade or more, this new manufacturing method, once perfected, has the potential to revolutionize design and manufacturing. Within the metal manufacturing industry, this form of 3-D assembly has become known as laser additive manufacturing (LAM). But instead of the “subtractive” techniques used in conventional machining of metallic or ceramic materials, in which material is progressively removed from a solid block to create a part, the part is progressively built up in 3-D via laser sintering or melting, using either a bed or stream of powdered material. It uses the same radiation source-high-power laser energy.

In the shadows of this first generation of laser-aided manufacturing, however, a second approach has been quietly maturing. LAM can produce complex turbomachinery components (top), customized joint implants (bottom) and an expanding range of other components.
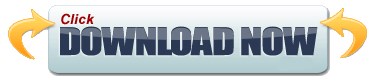